One of the real issues of Working at Height is that many people don’t realise a particular task is defined as ‘Working at Height’. As an example, there is a high risk of falls when climbing on plant and equipment for maintenance purposes. Without proper safety equipment and training, this would leave an employer in breach of the law.
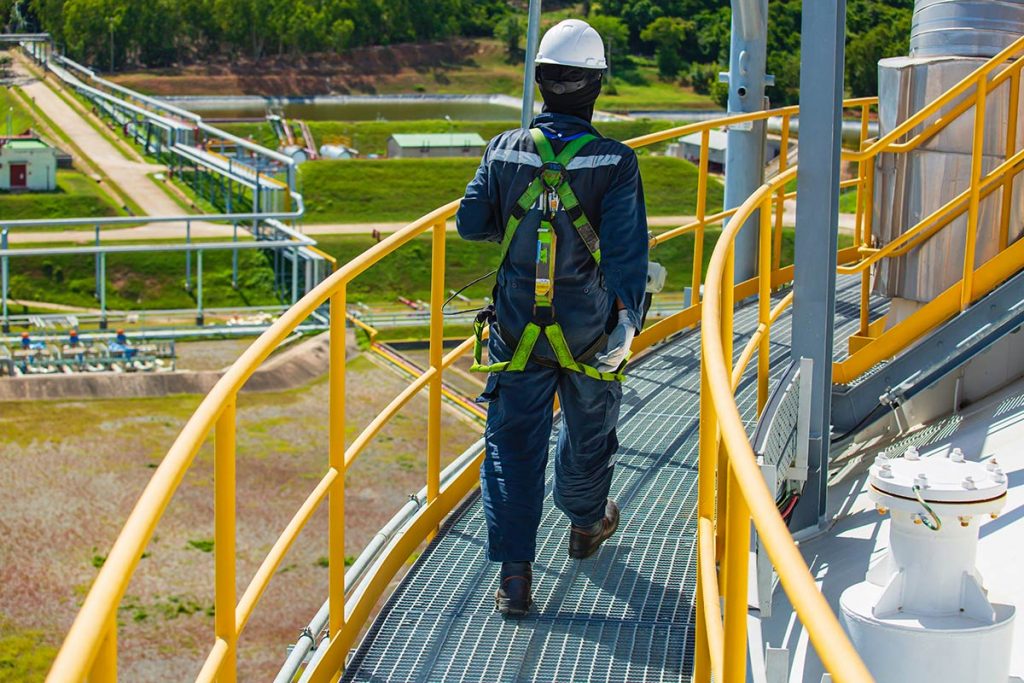
In this article, we’ll look at the implications of work at height regulations, carrying out proper risk assessments, the equipment that’s available to support safe working and the role that training plays in ensuring compliance with WAH regulations and keeping employees safe.
What is the definition of working at height?
There is no set height above which the work at height regulations come into force, so there is no hard and fast working at height definition. HSE (the Health and Safety Executive) states that ‘Work at height means work in any place where, if precautions were not taken, a person could fall a distance liable to cause personal injury’.
So you’re working at height if your work position is anywhere above ground or floor level, or where there is the potential for a fall from an edge or even into a hole in the ground. Equally, if there is any danger of falling through an opening or even through fragile surfaces which are not sufficiently load-bearing, the WAH regulations come into force.
Common Types of Working at Height
It’s important to remember that working at height can refer to locations both above ground and underground; it is the fall risk that defines the situation, no matter where the workplace is located.
Working at height can be as simple as using ladders to access a location or even standing on a chair to reach a higher level; there is always a risk of fall and injury. The regulations also cover working platforms like cherry pickers and booms, scissor lifts and scaffolding. In every situation, WAH regulations come into force and require the use of equipment and adequate training to keep people safe.
Requirements for employers
Any employer requiring employees to work at height is bound by law to ensure that the work is properly planned, correctly supervised and carried out by people with the right levels of competence – which is where training becomes so important.
At Reece Safety, we offer employers a ‘zero to compliance’ service, covering every aspect of WAH from an initial site survey through to training, equipment procurement, and risk assessment guidelines.
How many persons are required for work at height tasks?
The law allows you to work alone even if you are working at height. From a practical point of view, it is preferable to have a competent person on hand in the event of an incident. A separate rescue plan is mandatory by Law to allow a safe rescue from height and relying on dialling 999 would actually be in breach of the Law..
Implications for employers if employees aren't protected
Employers who fail to provide appropriate training and safety equipment, thereby breaching health and safety regulations, face consequences that include fines and even prison sentences. If an employer is deemed to have endangered human lives, the fines and sentences are unlimited. Damage to business reputation is also an important consideration
WAH Risk Assessment
A risk assessment looks carefully at the potential for harm for a person in a given work situation and sets out what controls should be put in place to prevent this. Risk assessments are carried out by persons who are deemed competent to evaluate the situation, exhibiting the right combination of knowledge, awareness, training and experience
Implementing a Risk Assessment
These usually follow five key criteria:-
- Identification of potential hazards
- Identification of who is at risk and what the risk may be
- Evaluation of these risks and decisions on what necessary precautions are required to mitigate them
- Recording the findings in a document and implementing them
- Revising risk assessments if any parameters change
Regulations and Guidelines
Alongside the Working at Height Regulations, there are a number of other bodies that play a role in ensuring people work in a safe manner.
OSHA and HSE Regulations and Guidelines
Occupational Safety and Health Administration (OSHA) is the UK’s national health and safety regulator. OSHA regulations and guidance tend to be black-and-white and prescriptive, telling you what you can and cannot do. The Health and Safety Executive (HSE) is Britain's national regulator for workplace health and safety, with regulations focusing more on risk assessment and ways to control risk at all levels.
Industry-Specific Regulations and Guidelines
Different industries also have requirements and recommendations, with WAH often crossing paths with other measures and other areas of legislation such as Lock Out Tag Out for electrical safety.
With extensive knowledge and experience in the world of personnel safety, Reece Safety offers a wide range of products and training courses developed to keep people safe and also to ensure employers are aware of their responsibilities and obligations.
Preparation Before Working at Height
The guidelines suggest that working at height should be avoided if at all possible, but in reality there are many situations where it is simply unavoidable. Important steps to take before working at height include:
- A competent person should carry out a risk assessment
- Prevent falls by selecting a place of work that is safe
- Act to minimise the consequences of falls by using the right type of equipment, properly inspected and maintained
Types of Equipment Used for Working at Height
Ladders and stepladders
What’s the difference? A ladder has rungs, whilst a stepladder has flat steps and often incorporates a platform to facilitate standing.
Scissor Lifts
Lifts with working platforms are used for elevating personnel, usually for safe maintenance routines.
Tower Scaffolds
Scaffolding with a series of support beams across its structure to provide additional rigidity and strength.
Mobile Elevated Work Platforms (MEWPs)
Mobile machines incorporating enclosed platforms are designed to move people to elevated working positions.
Fall Arrest Systems
A fall arrest system consists of equipment and components designed for differing situations and applications, protecting people when working at height. The system might include harnesses, lanyards, personal fall limiters (PFL) and rescue equipment.
Personal Protective Equipment (PPE)
Personal Protection Equipment that is specific to working at height will be determined by the risk assessment. Typical examples include work restraint systems, fall arrest systems and horizontal lifelines.
The Importance of Work Positioning
Work Positioning uses personal fall protection equipment to enable an individual to work safely at height, attached securely at two points so that any fall is prevented or restricted.
Work positioning techniques can be used to help people safely climb ladders to work areas, with temporary anchors safely secured at two anchor points to prevent the individual from falling backwards.
Reece Safety provides specialist work positioning training covering every aspect of the technique from inspection, donning, using and safe descent.
In Summary: The dos and don'ts of working at height
- Avoid working at height unless you absolutely have to!
- Make sure you have your risk assessment in place, properly managed
- Consult with specialists to implement your working protocols
- Invest in the appropriate safety equipment
- Invest in training from the management level to the operative level to ensure there is an enterprise-wide understanding of the implications of Working at Height
Reece Safety offers a comprehensive portfolio of specialist training and consultancy services for working at height, from survey to compliance. Tell us about your requirements – we can devise a package to match your needs.